Porosity in Welding: Identifying Common Issues and Implementing Ideal Practices for Avoidance
Porosity in welding is a pervasive problem that commonly goes undetected until it causes significant troubles with the stability of welds. This typical problem can jeopardize the strength and resilience of bonded structures, positioning safety and security threats and leading to expensive rework. By understanding the origin creates of porosity and executing reliable prevention techniques, welders can dramatically improve the quality and reliability of their welds. In this discussion, we will discover the crucial aspects adding to porosity formation, examine its destructive effects on weld efficiency, and discuss the most effective techniques that can be embraced to lessen porosity incident in welding procedures.
Common Reasons For Porosity
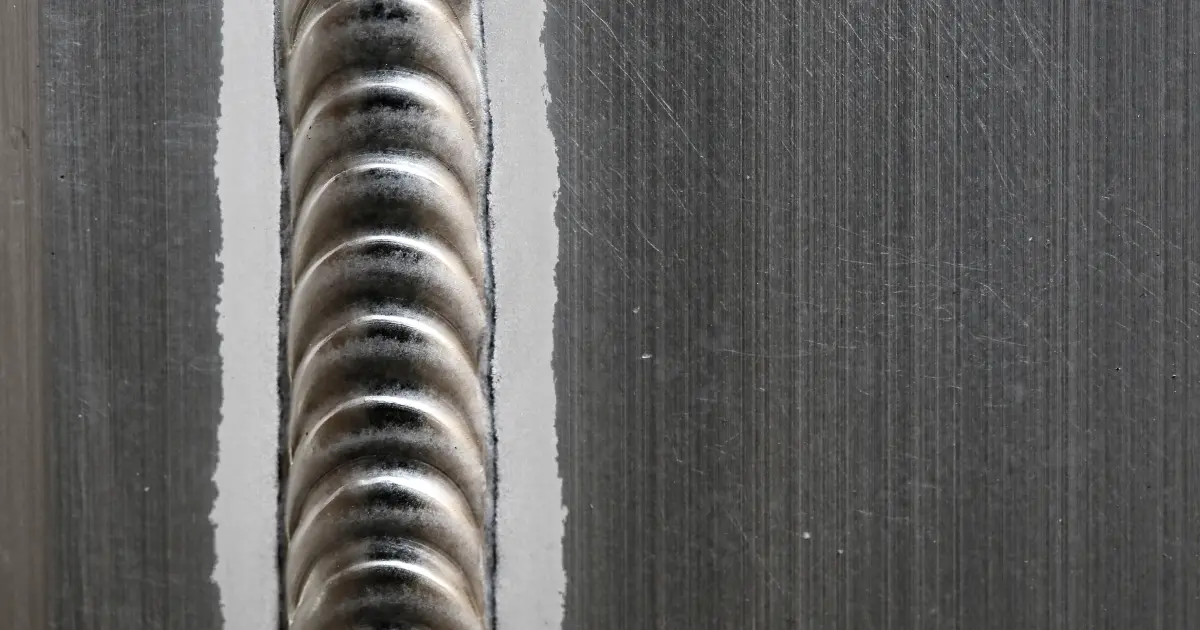
Another regular offender behind porosity is the presence of pollutants externally of the base steel, such as oil, oil, or rust. When these impurities are not successfully gotten rid of prior to welding, they can evaporate and become entraped in the weld, causing problems. Furthermore, making use of filthy or damp filler materials can introduce pollutants into the weld, adding to porosity issues. To mitigate these typical reasons for porosity, comprehensive cleaning of base metals, proper securing gas option, and adherence to optimal welding criteria are necessary methods in attaining high-quality, porosity-free welds.
Influence of Porosity on Weld Quality

The existence of porosity in welding can dramatically compromise the architectural stability and mechanical buildings of welded joints. Porosity develops gaps within the weld steel, weakening its total strength and load-bearing capability.
One of the primary repercussions of porosity is a reduction in the weld's ductility and sturdiness. Welds with high porosity levels tend to show lower impact strength and lowered capability to warp plastically prior to fracturing. This can be specifically concerning in applications where the welded parts go through vibrant or cyclic loading conditions. Furthermore, porosity can restrain the weld's capacity to properly transfer forces, leading to early weld failing and potential safety dangers in critical frameworks.
Finest Practices for Porosity Avoidance
To improve the structural honesty and high quality of welded joints, what details actions can be executed to decrease the occurrence of porosity during the welding procedure? Porosity avoidance in welding is vital you could try these out to make sure the honesty and strength of the last weld. One effective practice is proper cleaning of the base metal, getting rid of any pollutants such as rust, oil, paint, or moisture that could lead to gas entrapment. Guaranteeing that the welding equipment is in excellent problem, with tidy consumables and suitable gas circulation prices, can additionally considerably decrease porosity. In addition, keeping a secure arc and regulating the welding criteria, such as voltage, current, and take a trip speed, aids produce a constant weld pool that lessens the danger of gas entrapment. Making use of the proper welding method for the specific product being bonded, such as readjusting the welding angle and gun setting, can additionally prevent porosity. Regular assessment of welds and immediate remediation of any type of concerns recognized during the welding procedure are vital practices to stop porosity and generate top quality welds.
Value of Proper Welding Techniques
Carrying out appropriate welding methods is critical in making sure the structural integrity and quality of bonded joints, building on the structure of reliable porosity prevention measures. Welding methods directly affect the overall toughness and resilience of the welded framework. One key facet of correct welding strategies is websites preserving the appropriate heat input. Too much warmth can result in raised porosity because of the entrapment of gases in the weld swimming pool. On the other hand, insufficient heat may cause incomplete fusion, producing possible powerlessness in the joint. Furthermore, using the appropriate welding criteria, such as voltage, present, and travel rate, is vital for accomplishing audio welds with very little porosity.
In addition, the choice of welding process, whether it be MIG, TIG, or stick welding, ought to align with the certain needs of the job to make sure ideal outcomes. Appropriate cleaning and preparation of the base steel, along with choosing the best filler product, are likewise important elements of proficient welding strategies. By sticking to these best methods, welders can minimize the danger of porosity development and generate premium, structurally audio welds.
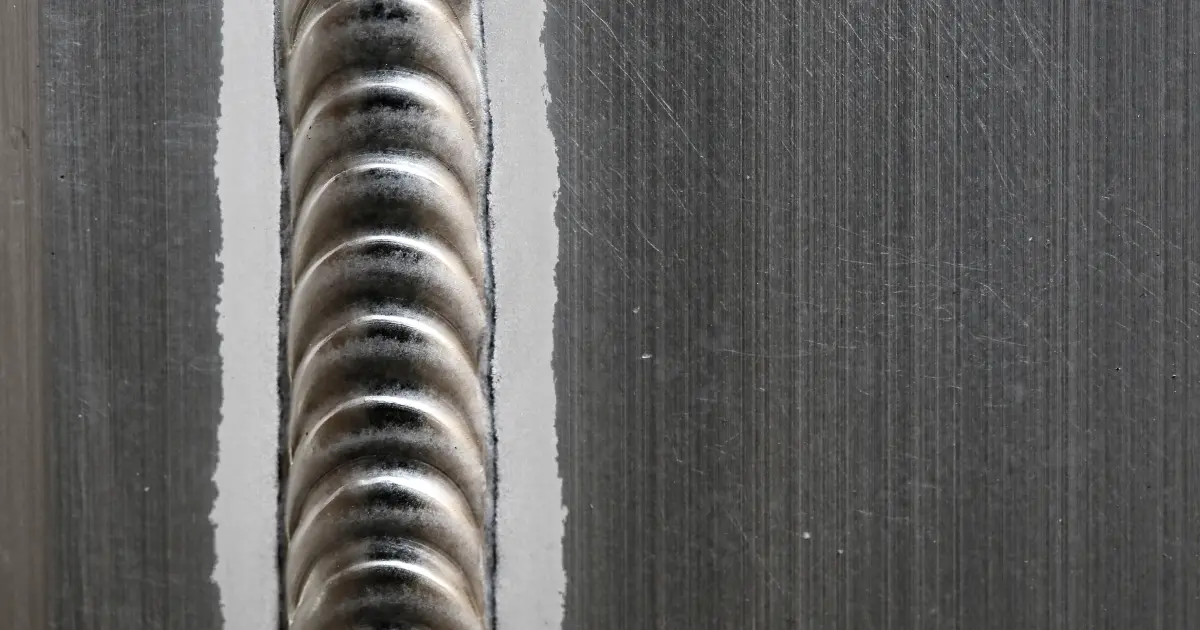
Testing and Quality Assurance Steps
Checking treatments are important to identify and prevent porosity in welding, making certain the stamina and sturdiness of the last item. Non-destructive screening techniques such as ultrasonic testing, radiographic screening, and aesthetic evaluation are commonly used to recognize possible flaws like porosity.
Performing pre-weld and post-weld assessments is likewise vital in keeping quality control standards. Pre-weld examinations entail confirming the materials, devices settings, and cleanliness of the workspace to stop contamination. Post-weld assessments, on the over at this website various other hand, examine the last weld for any type of defects, including porosity, and validate that it fulfills defined standards. Applying a detailed quality assurance strategy that includes thorough testing treatments and examinations is paramount to lowering porosity problems and guaranteeing the general high quality of bonded joints.
Final Thought
To conclude, porosity in welding can be a typical issue that affects the quality of welds. By determining the typical reasons of porosity and implementing best methods for prevention, such as appropriate welding methods and testing procedures, welders can guarantee premium quality and reliable welds. It is necessary to prioritize prevention methods to minimize the event of porosity and preserve the integrity of bonded frameworks.
Comments on “Just how to Determine What is Porosity in Welding and Improve Your Strategy”